Bulging Between Rolls in Continuous Casting
Brian Thomas, Lan Yu and Kuan-Ju Lin
Continuous Casting Consortium, China Steel
During continuous casting process, strands frequently experience bulging beneath the mold in the spray zone of a continuous caster, which is caused by internal ferrostatic pressure acting on the solidifying strand shell due to the weight of liquid steel and the height from the meniscus. Bulging is directly responsible for internal cracks, centerline segregation, and permanent deformation, which lead to poor quality of the continuously cast products. It can also cause an increase of the load transmitted to the rolls and enhance their rate of wear. In practice, it is important to estimate bulging quantitatively in continuous caster design and set-up of secondary cooling conditions, especially in high-speed casting.
In order to quantify and better understand the bulging phenomenon, 2-D Finite Element thermal stress Models (see the following figure) are being developed using ABAQUS.
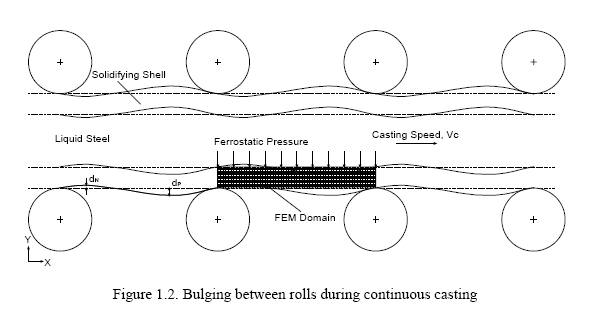
(click for a full-sized picture)
Wunnenberg Conditions:
Slab width = 1350 mm
Roll pitch = 860 mm
Shell thickness = 79 mm
T Liquidus = 1500 ° C
T Surface = 1000 ° C
Liquid steel density = 7000 kg/m3
Distance from meniscus = 3.9 m
Ferrostatic pressure = 0.26 MPa
Casting speed = 0.85 m/min (14.2 mm/s)
Results:
- Non-symmetric bulging profile with maximum bulging at about 65% from the upstream roll matches the measurements appearing in the literature.
- Negative bulging confirms the experimental observation.
- Heat transfer run has been incorporated into the model and temperature profile effect on bulging turns out to be small.
- Creep has a significant effect on bulging.
- Mesh refinement has been tried in order to get more accurate result, but it takes more time and storage. The following is a quick comparison of single cycle bulging simulations with different meshes.
Mesh |
CPU time |
Memory |
Storage |
Max deflection |
Coarse mesh (60x8) |
12 min. |
16M |
140 M |
5.7 mm |
Normal mesh (60x16) |
30 min. |
17M |
200 M |
6.2 mm |
Fine mesh (120x20) |
500 min. |
22M |
2.5 G |
7.5 mm |
Future Plan:
- Continue model development by improving mechanical property models until a reasonable match with Wunnenberg measurement is obtained.
- Try other cases to confirm our model.
- Perform parametric study on wide-face bulging and find an equation to predict bulging as a function of roll pitch, temperature, shell thickness, ferrostatic pressure, casting speed and material. It may need more time than code development.
- Extend model to predict transient behavior with consideration of roll pitch changes, casting speed changes, etc.
Publications:
Lan Yu, "FEM Analysis of Bulging between Rolls in Continuous Casting", MS Thesis, University of Illinois, 2000.
Thomas, B.G.; "Modeling of the Continuous Casting of Steel: Past, Present and Future", Metall. Mater. Trans. B, Vol. 33B, Dec., 2002, pp. 795-812; (Dr. J. Keith Brimacombe Lecture, 2001, Iron and Steel Society; reprinted from 59th Electric Furnace Conference Proceedings, Nov. 11-14, 2001, Pheonix, AZ, ISS, Warrendale, PA, pp. 3-30). Click here for a PDF version. (2.10 MB)
Lin, Kuan-Ju and B.G. Thomas, "Thermal Stress Analysis of Bulging with Roll Misalignment for Various Slab Cooling Intensities", China Steel Technical Reports, No. 16, 2002, pp. 9-14.
|