Influence of Mold Geometry on Mold Temperature in Continuous Cast Steel
Brian Thomas and Melody Langeneckert
Continuous Casting Consortium
Three-dimensional finite-element models using ANSYS have been used to study the relationship between mold geometry and heat transfer. Three-dimensional calculation results have been distilled into simple analytical relationships. Specifically, the narrow face corner temperature can be predicted easily for different cooling water slot geometries, in order to identify ways to achieve uniform hot face temperature (such as to avoid corner crushing, fin defects, and sticker breakouts). A simple relation to relate thermocouple measurements to heat flux has been incorporated into an existing heat transfer model, CON1D, using the concept of offset distance. This model can be applied to study the cause of crack defects in continuous cast steel, especially those related to changes in water-cooled copper mold design and associated changes in thermocouple signals.
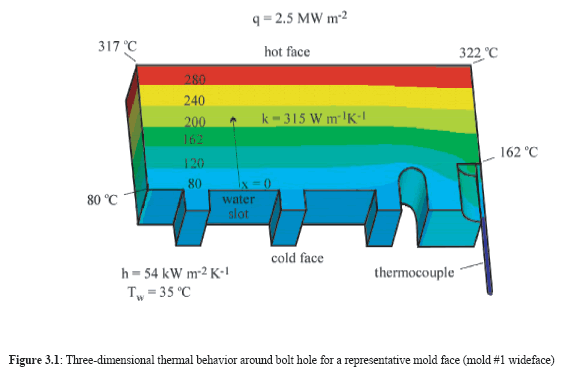
Publications:
Melody Langeneckert, "Influence of Mold Geometry on Heat Transfer, Thermocouple and Mold Temperatures in the Continuous Casting of Steel Slabs," MS Thesis, University of Illinois, 2001.
Thomas, B. G., M. Langeneckert, L. Castellá, M. Dziuba, G. Di Gresia, and W. Balante; "Optimisation of Narrow Face Water Slot Design for Siderar Slab Casting Mould", Ironmaking and Steelmaking, Vol. 30, No. 3, 2003, pp. 235-239. Click here for a PDF version (585 KB).
|