(NSF) GOALI: Online Dynamic Control of Cooling in Continuous Casting of Thin Steel Slabs (2005-2008)
B.G. Thomas, J. Bentsman, S. Vapalahti, K. Zheng, B. Petrus, H. Li, H. Castillejos, and F. Acosta
National Science Foundation GOALI DMI 05-00453, Continuous Casting Consortium
National Science Foundation Support
DMI 05-00453
5/1/2005 to 4/30/2008
NSF Program Director: Mary Reallf, (703) 292-7088
NSF Grants Official: Denise M. Giles, (703) 292-8212
Industry Support and Partnerships
Nucor Steel, Decatur, Alabama
Nucor Steel is the GOALI Industry partner of this project. We are implementing and testing our new models in their plant first, with their help and support.
Cinvestav
Cinvestav has provided most of the laboratory experimental equipment for measuring the heat transfer coefficients during spray cooling.
Continuous Casting Consortium
The Continuous Casting Consortium provided partial matching funds to the project. Students worked on projects related to both this project and to the center.
Delavan Spraying
Technologies, Monroe, NC, and Spraying Systems, Wheaton, Illinois
Both of these companies have supplied technical information on the spray nozzles used in continuous casting machine secondary cooling systems, needed to help our fundamental model investigations, in addition
to funds for related student projects in the area.
Project Summary
Temperature variations during cooling cause quality problems such as cracks, especially under transient conditions such as caused by changes in casting speed. Setting the spray water flow rates to maintain optimal temperature profiles during process changes becomes increasingly difficult when the casting speeds are high and response times must be fast. This project aimed to develop a fundamentally-based online system to dynamically control the water flow rates in order to continuously optimize and stabilize cooling conditions in the thin slab casting process. The system used model-based predictive control, incorporating both online measurements of mold heat removal and on a high-speed finite-difference model of heat conduction and solidification during the process.
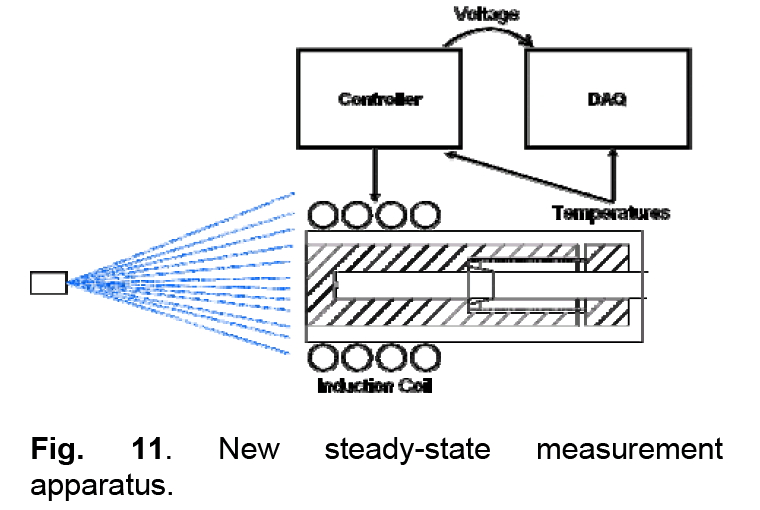
Summary of Activities
Click here for full Activities PDF
(615 KB)
In this multifaceted project to improve control of spray cooling
heat transfer in continuous casting of steel with the aid of fundamentally-based
models, research activities proceeded on several different subprojects:
1) Efficient fundamental model of solidification and temperature in thin slab casting: CON1D
The control system is based on a software sensor, which is based on a solidification model developed in previous
work, CON1D. Modifications made to the CON1D model as part of this project include:
a) Changing the modeling of heat transfer in the mold to force the total heat flux to match the measured input value;
b) Incorporating the increase in heat transfer that occurs during nucleate boiling, according to the Leidenfrost
temperature;
c) Mesh and time-step studies were performed to optimize the program to run faster to enable it to serve as part of a
real-time control model.
d) Extending the model to simulate both inside and outside of the strand, as it was found that heat transfer was
different in these 2 regions, and this affects both the temperature, and the final solidification point.
e) In addition to successful model-based prediction and control capability, the model was used to generate setpoints
for typical casting conditions. Specifically, 72 set points were generated for the Nucor caster to allow operation at 8
different spray-water patterns over a range of casting speeds (discretized as 9 different speeds over the maximum speed range). These set points are temperature profiles generated by CON1D using typical mold heat flux dependent
on casting parameters which includes casting speed.
2) Software Sensor, CONONLINE
In this project, the CON1D model described in the previous section has been adapted to serve as a “software sensor”
in place of hardware temperature sensors for use in the control system. Traditional feedback control of the
secondary cooling sprays has not been implemented in commercial casters, primarily due to the difficulty of
operating sensors in the spray region. Optical pyrometers can be inaccurate due to emissivity variations from
intermittent surface scale on the steel and diffraction through the water spray and steam. Even with reliable
pyrometers, open-loop model-based estimation still would likely be needed to fill the gaps between their highlylocalized
readings to attain reasonable performance.
3) Online control system development
A control system has been developed that integrates with the Level 2 system of a continuous caster, to control the
spray water cooling flow rates in real time. The software implementation of this system includes
1) The software
sensor CONONLINE
2) A monitor to display the results in real time, and to manually enter temperature setpoint
profiles (as desired)
3) A control algorithm CONCONTROLLER to regulate the surface temperature, in addition
to network software to maintain communications and shared memory.
4) Laboratory measurement of water flow and heat transfer during spray
cooling
Experiments have been initiated as part of this project to gain a more fundamental understanding of water spray
cooling at high temperatures. The research focuses on the conditions found at the surface of the steel strand in the
secondary spray cooling zones of steel continuous casting machine with water jet / air mist or “pneumatic” cooling.
These conditions include a steel surface temperature range of 1300-700°C.
5) Steel plant experiments for model validation
Experimental trials have been carried out at Nucor Steel, Decatur, Alabama, and at Mittal Steel, Riverdale, in order
to measure slab surface temperature variations with optical pyrometers. In addition, mold heat flux is measured from
the temperature rise of the cooling water, knowing the water flow rate. These results have been used to calibrate the
CON1D model (and thereby also CONSENSOR for CONONLINE).
6) Understanding defect formation during continuous casting
To gain maximum benefit from a new spray-water control system, it is important to have a fundamental
understanding of how defects form in the process. Parallel research is ongoing to achieve this aim. Work has been
initiated to gain new insight into the mechanism of formation of defects associated with secondary spray cooling.
These surface defects often initiate in the mold, especially at the meniscus, and later form surface cracks far
below the mold in the secondary spray cooling zones. Cracks form at the roots of oscillation marks, which are prone
to transverse crack formation during the spray cooling, depending on the temperature history, and the formation of
embrittling precipitates. Thus, oscillation mark depth, hook formation, and other defects are also being studied. As
a first step to predict precipitate formation, a model has been developed, based on fundamental simulation of particle
growth from individual molecules to real precipitates, using a size-grouping model approach.
7) Control of mold fluid flow
Many casting defects are caused by problems with fluid flow and heat transfer in the mold. To control fluid flow in
the mold, an electromagnetic brake (EMBr) force is applied in many thin slab casters, including Nucor. A
computational fluid flow model has been developed and applied to investigate the effects of varying SEN
submergence depth and EMBr field strength on flow in the mold cavity. The three-dimensional, steady k-e
model of the nozzle and liquid cavity in the mold used the magnetic induction method in FLUENT to incorporate
8
the localized-type static EMBr field measured at a steel plant. This model can be used to predict optimal operation
of the EMBr to minimize fluid flow problems. Combined with better control of spray cooling below the mold, the
overall quality of the continuous-cast product can be improved.
8) Advance Control Algorithm Development
Research in online control algorithms will lay the foundation for improved optimal prediction and predictive control
of systems governed by the nonlinear parabolic PDEs that describe continuous casting.
Summary of Findings Click here for full Findings PDF (1.08 MB)
A new online computer model-based control system has been created to control
solidification and temperature development during the continuous casting
of steel. It features an accurate and fundamentally-based dynamic software
sensor of the spray-cooling region which is integrated with online measurements
of mold heat extraction and other process parameters. By maintaining the
steel temperature through operational transients, this system has aimed
to enable faster and more efficient casting with improved quality of the
steel product. This multi-faceted research project includes the development,
validation, and calibration of the online control models, laboratory measurements
to better characterize heat transfer during spray cooling, improved control
algorithms, and increased understanding of defect formation in the continuous
casting process. The research done has obtained several new findings,
which are significant to the project goals. Most significant are:
1) A novel modeling algorithm is able to update in real time, the complete
solidification and temperature profile in two dimensions at every second
during continuous online operation.
2) The new control system maintains temperature more closely than the conventional
control system currently in use at most plants. This new modeling tool is now available to study thin-slab casting behavior,
to enable future process and control improvements. 3) Better understanding of the control of defects arising during continuous
casting has been achieved, including the control of fluid flow in the
mold using electromagnetic braking, and cracks associated with the control
of secondary cooling.
4) New optimal control algorithms have been developed, with application
to the systems and equations governing heat transfer in continuous casting.
Future improvements to this novel model-based control system should revolutionize the control of continuous casting spray systems, with improved steel quality, and will have beneficial impact on related scientific fields and commercial processes.
NSF Publications
Kim, J. and J. Bentsman, "Robust Adaptive Control of Parabolic and Hyperbolic Systems with Spatially-varying Parameters," 44th IEEE Conference on Decision and Control, (Seville, Spain, Dec. 13-15, 2005), 2005, 1503-1508.
Kim, J. and J. Bentsman, "Multiresolution Finite-Dimensionalization of Parameter Update Laws in Adaptive Control of Distributed Parameter Systems," 45th IEEE Conference on Decision and Control, (San Diego, CA, Dec. 13-15, 2006), 2006, 2801-2806.
Kim, J. and J. Bentsman, "Disturbance Rejection in Robust Model Reference Adaptive Control of Parabolic and Hyperbolic Systems," 45th IEEE Conference on Decision and Control, (San Diego, CA, Dec. 13-15, 2006), 2006, 3083-3088.
Thomas, B. G., J. Bentsman, B. Petrus, S. Vapalahti, H. Li, A. H. Castillejos, and F. A. Acosta, “GOALI:
Online Dynamic Control of Cooling in Continuous Casting of Thin Steel Slabs,” Proceedings of 2008 NSF
CMMI Engineering Research and Innovation Conference, Knoxville, Tennessee, 16p., Jan. 7-10, 2008.Click here for a PDF version. (623 KB)
Zheng, K., B. Petrus, B.G. Thomas, and J. Bentsman, “Design and Implementation of a Real-time Spray
Cooling Control System for Continuous Casting of Thin Steel Slabs”, AISTech 2007, Steelmaking
Conference Proc., (May 7-10, Indianapolis, IN), AIST, Warrendale, PA, Vol. 1, 2007. Click here for a PDF version (1.53 MB)
|